Introduction
Control cable termination is a critical aspect of electrical and electronic installations, ensuring efficient transmission of signals and power between devices. Proper termination not only ensures signal integrity but also enhances the overall reliability and performance of the system. In this comprehensive guide, we will delve into the various aspects of control cable termination, including its importance, types of terminations, best practices, common mistakes to avoid, and tips for achieving optimal results.
Importance of Control Cable Termination
Control cables are used in a wide range of applications, including industrial automation, telecommunications, audio-visual systems, and more. These cables carry signals or power from one device to another, making them essential components of any interconnected system. Control cable termination refers to the process of connecting the cable to the devices it serves, typically through connectors, terminals, or other termination points.
Proper termination is crucial for several reasons:
1. Signal Integrity: Control cables carry sensitive signals that can be easily affected by external interference, such as electromagnetic interference (EMI) or radio frequency interference (RFI). Proper termination helps to minimize these interferences, ensuring that the signals reach their intended destination without distortion or loss.
2. Reliability: A well-terminated control cable provides a secure and stable connection between devices, reducing the risk of signal loss, intermittent connections, or other issues that can lead to system failures or malfunctions.
3. Performance: Proper termination can optimize the performance of the entire system by ensuring that signals are transmitted efficiently and accurately. This is particularly important in high-speed data transmission applications where signal integrity is paramount.
Types of Control Cable Terminations
Control cable termination can be achieved using various methods and connectors, depending on the specific requirements of the application. Some common types of control cable terminations include:
1. Soldering: Soldering is a traditional method of terminating control cables by melting a solder alloy to create a permanent bond between the cable conductor and the termination point. Soldered connections are known for their reliability and durability, making them ideal for high-stress applications.
2. Crimping: Mineral Insulated Cable involves using a specialized tool to compress a metal sleeve or ferrule onto the cable conductor and the termination point. This method is popular for its ease of use, speed, and repeatability, making it suitable for mass production or field installations.
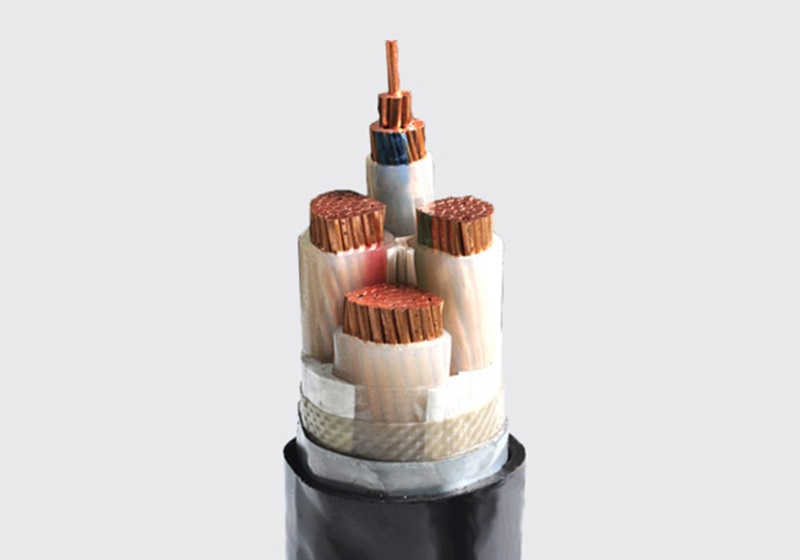
3. Compression: Compression terminations use a compression tool to secure a connector onto the cable conductor, creating a tight and reliable connection. Compression terminations are commonly used in coaxial cables and other high-frequency applications.
4. Insulation Displacement Connection (IDC): IDC terminations involve piercing the insulation of the cable to make a connection with the conductor inside. This method is often used in flat cables or ribbon cables where individual conductors need to be terminated quickly and efficiently.
5. Screw Terminal: Screw terminals are used to terminate control cables by clamping the cable conductor between a screw and a terminal block. This method allows for easy installation and removal of cables, making it suitable for applications that require frequent changes.
Best Practices for Control Cable Termination
To ensure a successful control cable termination, it is essential to follow best practices and industry standards. Here are some tips for achieving optimal results:
1. Use the Right Tools: Investing in high-quality tools and equipment is essential for achieving reliable and consistent terminations. Make sure to use tools that are specifically designed for the type of termination you are performing, whether it is soldering, crimping, compression, or others.
2. Follow Manufacturer's Instructions: Always refer to the manufacturer's instructions for both the cable and the termination components to ensure proper installation. Each type of cable and connector may have specific requirements that need to be followed for a successful termination.
3. Prepare the Cable Properly: Before terminating the cable, make sure to strip the insulation carefully to expose the required length of the conductor. Avoid nicking or damaging the conductor during the stripping process, as it can lead to poor connections or signal loss.
4. Ensure Proper Alignment: When terminating the cable, ensure that the conductor is properly aligned with the termination point to avoid any misalignment or short circuits. Misaligned connections can result in signal distortion or damage to the equipment.
5. Test the Termination: After completing the termination, it is important to test the connection to ensure that it is secure and functional. Use appropriate testing equipment to verify continuity, signal integrity, and insulation resistance.
Common Mistakes to Avoid
While proper control cable termination is crucial for system performance, there are common mistakes that can lead to issues such as signal loss, intermittent connections, or even equipment damage. Here are some common mistakes to avoid when terminating control cables:
1. Overheating during Soldering: Overheating the cable conductor during soldering can damage the insulation or weaken the conductor, leading to poor connections or signal loss. Use the correct soldering temperature and technique to avoid overheating.
2. Incorrect Crimping: Improper crimping can result in loose connections, poor contact, or conductor breakage. Make sure to use the right crimping tool and follow the manufacturer's guidelines for crimping terminals to achieve a reliable connection.
3. Using the Wrong Connector: Using a connector that is not compatible with the cable type or size can lead to poor connections or signal distortion. Always select connectors that are designed for the specific cable and application to ensure proper termination.
4. Poor Cable Stripping: Inadequate cable stripping can result in insufficient contact between the conductor and the termination point, leading to signal loss or intermittent connections. Take care to strip the cable insulation evenly and without damaging the conductor.
5. Lack of Proper Testing: Failing to test the termination after installation can result in undetected issues that may cause problems later on. Always perform thorough testing to ensure that the connection is secure and functional before putting it into service.
Conclusion
Control cable termination is a critical aspect of electrical and electronic installations, with a direct impact on system performance and reliability. By following best practices, avoiding common mistakes, and using the right tools and techniques, you can achieve successful terminations that ensure optimal signal integrity and system functionality. Whether you are working on industrial automation, telecommunications, or any other application that relies on control cables, mastering the art of cable termination is essential for achieving efficient and reliable system operation.